Эксплуатационные особенности роликового подшипника. |ЧАСТЬ 2|
Дополнительные параметры, которые следует учитывать при выборе подшипника.
Требуемая минимальная нагрузка на подшипники качения.
Подшипники качения могут выходить из строя преждевременно из-за чрезмерной или недостаточной нагрузки. Этот эффект обусловлен кинематическими характеристиками подшипников качения. Подвижные элементы подшипников, работающих на высоких скоростях, выталкиваются наружу центробежными силами. Вот почему требуется минимальная нагрузка, чтобы поддерживать вращающиеся элементы, вращающиеся вдоль и вокруг дорожек качения оптимальным образом, не создавая чрезмерного трения скольжения.Для механизмов, где подшипники не достигают этой требуемой минимальной нагрузки, происходит трение скольжения, что приводит к чрезмерному износу и сокращению срока службы. Подшипники, работающие в условиях высоких скоростей или сильных вибраций, особенно подвержены повреждениям. Когда происходит чрезмерное трение скольжение, смазочный слой между компонентами подшипника может быть сдвинут в результате металлического контакта. Этот контакт вызывает мазки на беговых поверхностях. Получаемый урон даст заметный более высокий уровень шума, и более грубую работу с высокими вибрациями. Другим признаком такого явления может быть быстро растущая рабочая температура, что в конечном итоге приводит к отказу подшипника.
Минимальная нагрузка для обеспечения удовлетворительной ходовой производительности зависит от используемого типа подшипника и от конкретной скорости работы. В подавляющем большинстве механизмов требуемая минимальная нагрузка уже будет достигнута за счет веса валов и других деталей в узле подшипника. Некоторые типы подшипников особенно упорные подшипники очень чувствительны к условиям недостаточной нагрузки из-за их кинематической характеристики. Конкретная информация о минимальной нагрузке, требуемой для упорных подшипников, приведена в отдельных таблицах информации о продуктах. Для радиальных подшипников могут применяться следующие значения для минимальной нагрузки:
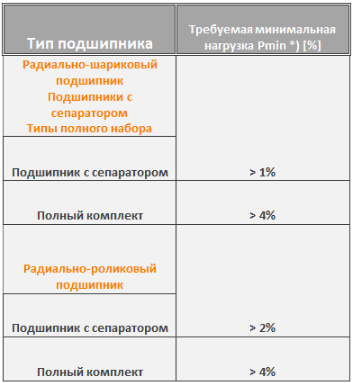
*) Рекомендуемая минимальная нагрузка задается в процентах от номинальной динамической нагрузки Cr
Влияние рабочей температуры.
Динамические нагрузки на подшипники качения рассчитываются с использованием системы, находящейся в стандарте DIN ISO 281. Этот расчет предполагает определенную твердость подшипниковых колец и элементов качения, обычно изготовленных из хромовой стали.Для всех подшипников качения NKE требуемая твердость гарантируется стандартной термической обработкой колец и элементов качения.
В всяком случае будут наблюдаться значительные изменения рабочих температур в структуре несущей стали. Это может изменить размерную и геометрическую точность несущих колец и включить потерю жесткости компонентов. Впоследствии снижается номинальная нагрузка подшипника.
Во время расчета подшипника необходимо учитывать эту потерю в рейтинге нагрузки.
Стандартная термическая обработка подшипников качения NKE обеспечивает стабилизацию размеров при постоянной рабочей температуре + 120 °C. Допускаются кратковременные пиковые значения до + 150 °C, которые не влияют на производительность подшипника. Поскольку эта термообработка стандартная, специальной маркировки на подшипнике не делается.
Подшипники, подверженные постоянным более высоким рабочим температурам, требуют специальной термообработки их колец. Такие подшипники NKE доступны по заказу, хотя необходимо учитывать пониженную грузоподъемность.
Чтобы определить снижение динамической нагрузки, применяемая формула в сочетании с коэффициентом уменьшения температуры, указанным в таблице.
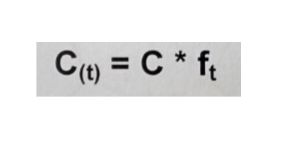
где
C (t) = приведенная динамическая грузоподъемность, кН
C = рейтинг динамической нагрузки, указанный в таблицах продуктов, кН
Cr для радиальных подшипников
Ca для упорных подшипников
f (t) = коэффициент снижения температуры
Коэффициент снижения температуры:
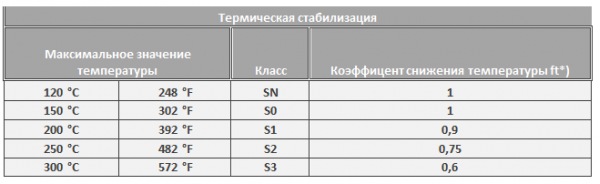
Внимание:
В случае подшипников для высокотемпературных процессов в механизмах, смазка, уплотнение и конструкция подшипника должны быть тщательно отрегулированы. Кроме того, при работе с посадочными подшипниками также необходимо учитывать допустимый температурный диапазон уплотнений подшипников и смазки.
Расчет номинального срока службы осциллирующих подшипников:
В некоторых случаях подшипники не вращаются, а выполняют только колебательные движения.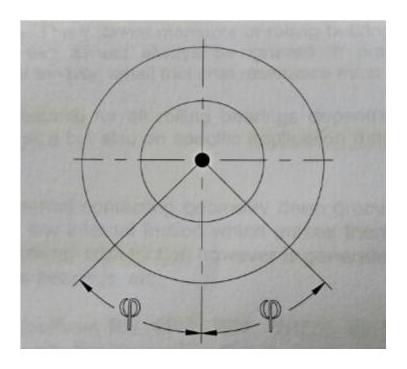
Расчет номинальной мощности приведен ниже:
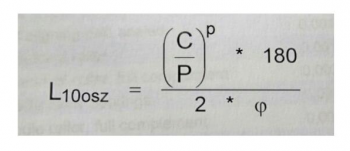
p = показатель срока службы
для шариковых подшипников: p = 3
для роликовых подшипников: p = 10/3
L (10osc) = номинальный рейтинг для колебательного движения, 10 ^ 6 движений
C = динамическая грузоподъемность, кН
Cr для радиальных подшипников
Ca для упорных подшипников
P = максимальная эквивалентная несущая нагрузка, кН
φ = половина осциллирующей амплитуды, град.
Трение в подшипниках качения.
Очень низкое внутреннее трение является одной из основных характеристик подшипников качения. Фракционные моменты подшипников качения обычно настолько малы, что их практически всегда можно игнорировать на практике. Однако для некоторых механизмов необходимо учитывать даже небольшое сопротивление трению.Сопротивление трения для всех подшипников зависит не только от типа и размера подшипника, но и от конкретных данных механизма, таких как скорость, нагрузка и смазка.
Из-за того, что у шарикоподшипников есть глубокий паз они в целом имеют очень низкое внутреннее сопротивление, что делает их пригодными для высоких скоростей. Однако у некоторых типов подшипников, таких как цилиндрические роликовые подшипники и т.д., присутствует сравнительно высокое трение.
Контактные уплотнения (суффиксы RS, 2RS, RSR, 2RSR и т.д.) всегда создают дополнительное трение из-за предварительной загрузки их уплотнительных губ. Сепараторы (суффиксы Z, 2Z) работают как бесконтактные зазорные уплотнения с внутренним кольцом и впоследствии не генерируют дополнительного трения.
Дополнительное трение всегда создает дополнительное тепло. Именно поэтому максимальная рекомендуемая скорость уплотнительных подшипников ниже, чем у не уплотнительных подшипников.
Оценка фрикционного момента и обеспечение результатов достаточной практической точности возможны, применяя следующую формулу:
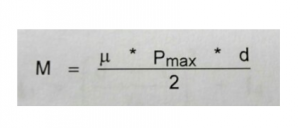
M = момент трения, Н*мм
μ = коэффициент трения
Pmax = максимальная загружаемая нагрузка подшипника, кН
d = диаметр отверстия, мм
Трение уплотнительных подшипников.
Подшипники с контактирующими уплотнениями (суффикс RS, 2RS, RSR, 2RSR и т.д.) всегда имеют более высокое трение из-за предварительной загрузки их уплотнительных губ, касающихся внутреннего кольца.Это дополнительное трение можно оценить, используя следующую формулу:
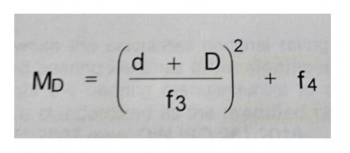
где
M (D) = дополнительный момент трения из-за контактных уплотнений, Н*мм
d = диаметр отверстия подшипника, мм
D = наружный диаметр подшипника, мм
f3, f4 = коэффициент, зависящий от типа
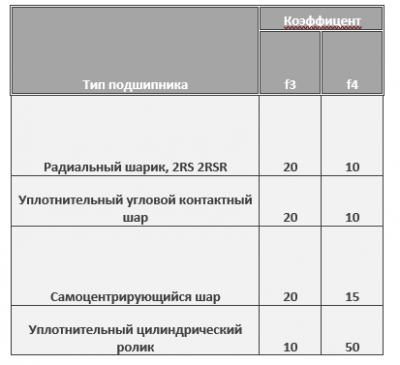
Это расчетное суммарное трение герметичного подшипника равно приблизительно:
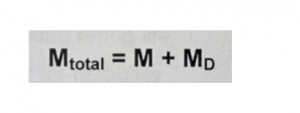
Точность значений, найденных с использованием приведенной выше формулы, достаточна для общего практического использования.
Модифицированный метод расчета срока службы.
Сравнение между рассчитанными номинальными значениями жизненного цикла и фактическим временем жизни подшипников значительно отличается. Это привело к тому, что производители подшипников применили современные методы расчета, которые были стандартизированы как измененный расчет срока службы по последнему стандарту: вместо ISO 281: 2007 стал использоваться DIN ISO 281: 2010.Расчет расширенного срока службы учитывает и оценивает влияние качества материала и условий эксплуатации.Эти влияния заключаются в следующем:
- надежность
- состояние смазки
- загрязнение
- прочность материала подшипника
Формула, которая будет использоваться для расчета расширенного срока службы Lnm:
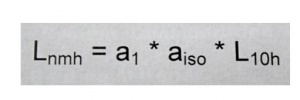
или
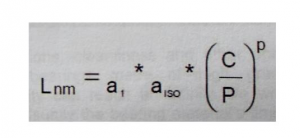
Lnmh = увеличенный срок службы, час
Lnm = расширенный срок службы, 10 ^ 6 rev
a1 = коэффициент надежности
aiso = коэффициент для комбинированного рассмотрения смазки, материала подшипника, загрязнения.
Фактор надежности a1.
Расчет номинального срока службы подшипника с использованием стандартизованного метода предполагает надежность 90%. Это означает, что в группе идентичных подшипников, работающих в тех же условиях, существует потенциал 10%, не достигающий расчетного срока службы. Однако практические опыты доказали, что более половины всех подшипников превышают рассчитанный срок службы до 5 раз. Обычно для общей техники приемлема надежность в 90%; в других случаях может потребоваться более высокая надежность с последующей повышенной безопасностью. Это может быть достигнуто с использованием коэффициентов надежности a1, перечисленных в таблице.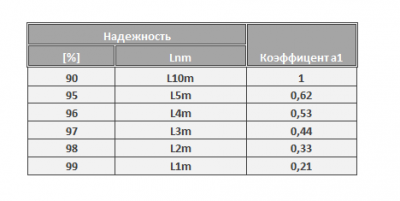
Очевидно, что для того, чтобы обеспечить максимальную надежность (L1m), значение срока службы будет уменьшено до 1/4 от стандартного, рассчитанного на 90% надежности (L10 м).
Фактор a iso для системного рассмотрения смазки, загрязнения, материала подшипника.
Если условия смазки, чистота и другие условия эксплуатации являются благоприятными, подшипники NKE из высококачественных сталей и высокое качество изготовления могут достичь бесконечного срока службы при экспонировании ниже определенного уровня нагрузки. Обычно предельная прочность на растяжение подшипника достигается, когда контактное давление верхнего загруженного элемента качения составляет около 1500 МПа. Соответствующая несущая предельная нагрузка Cu определяется типом подшипника, конструкцией внутреннего подшипника, профилем прокатных элементов и материала.Одним из наиболее важных требований к удовлетворительной функции подшипника качения является правильный выбор смазки.
Основная задача смазки в подшипнике состоит в том, чтобы отделить металлические части подшипника друг от друга.
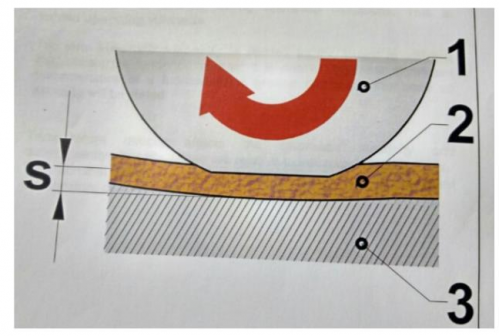
Стандартная формула для расчета номинального срока службы подшипника предполагает хорошее качество, чистую смазку, обеспечивающую достаточное разделение частей подшипника. Такое разделение будет достигнуто только тогда, когда смазочный слой (2) встанет между опорными кольцами (3) и элементами (1) качения, чтобы отделить смежные поверхности.
Поэтому слой смазки должен иметь толщину (s) больше, чем сумма шероховатости поверхности (Ra) или (1/2 Ra).Кроме того, никакие другие посторонние частицы или примеси не загрязняют смазку.
Наращивание смазочного слоя в подшипнике в основном зависит от консистенции смазки во время работы. Это называется рабочей вязкостью.
Термин кинематическая вязкость определяется как степень, в которой жидкость сопротивляется тенденции течь. Это одна из самых важных характеристик смазки. Для базовых смазок будет указана вязкость используемого масла.
Температура непосредственно влияет на вязкость масла / смазки, а последующие значения вязкости зависят от индивидуальных температур. Номинальное значение вязкости (v40) основано на температуре окружающей среды 40 °C.Требуемая минимальная вязкость смазки во время работы зависит от следующих факторов:
- размер подшипника
- рабочая температура
- скорость вращения
Простая и в целом точная оценка влияния смазки на расчетный срок службы подшипника возможна с использованием следующих диаграмм и инструкций:
1. Расчет среднего диаметра подшипника dm
2. Оценка требуемой рабочей вязкости v1
3. Определение фактической рабочей вязкости v
4. Построение отношения требуемой к фактической рабочей вязкости k
5. Оценка коэффициента a iso.
Эти шаги подробно объясняются в следующем примере:
Пример:
Определите коэффициент вязкости k для шарикоподшипника с глубоким пазом типа 6210 (диаметр отверстия 50 мм, наружный диаметр 90 мм)
Условия эксплуатации:
скорость n = 1000 об / мин
рабочая температура tmax = 70oC
Планируемая смазка с номинальной вязкостью v40 = 68 мм ^ 2 / с, и нормальной чистотой.
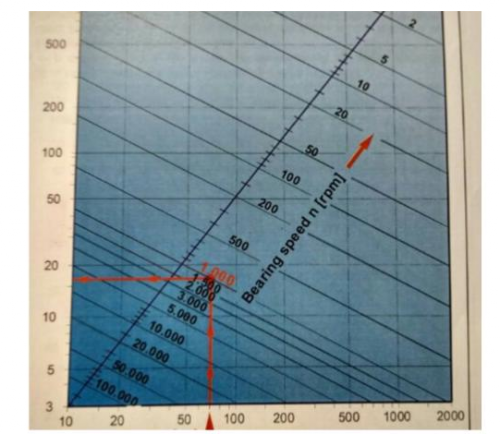
Шаг 1:
Рассчитайте диаметр подшипника с шагом d: dm = (d + D) / 2 = (50 + 90) / 2 = 70 мм
Шаг 2:
Нарисуйте линию на диаграмме по оси X, начиная с диаметра dm = 70 мм. Идите прямо вверх, пока линия не пересечет требуемую скорость, в этом примере скорость 1000 об / мин.
Из этой точки перейдите прямо к шкале, расположенной слева от диаграммы, где может быть найдена требуемая номинальная вязкость v1 для отдельных рабочих условий. В фактическом примере v1 составляет приблизительно 16мм^2/с.
v-t-диаграмма
Динамическая вязкость смазки зависит от температуры. Минеральные масла становятся более тонкими при более высоких температурах. Это означает, что вязкость уменьшается. При низких температурах смазочные материалы становятся более жесткими. Их вязкость увеличивается относительно их номинальной вязкости v40. Различные базовые масла реагируют по-разному с температурой и другими изменениями, поэтому вязкость масел и смазок зависит от другого. V-t-диаграмма показывает корреляцию более общих значений номинальной вязкости v40 для смазочных материалов на основе масел.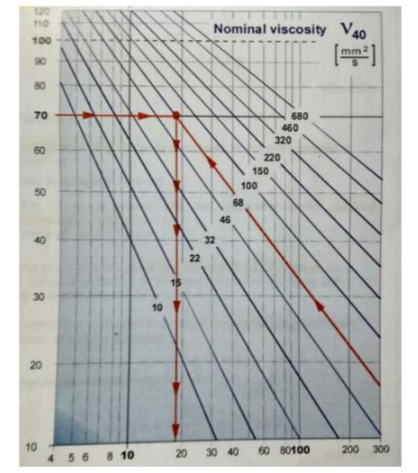
Шаг 3:
Следуйте линии кинематической вязкости масла v40 = 68 мм ^ 2 / с на диаграмме до пересечения линии, представляющей рабочую температуру t = 70oC. Отдалите линию вниз к горизонтальной оси, чтобы получить вязкость v для этой рабочей температуры. В этом примере рабочая вязкость v составляет приблизительно 18 мм ^ 2 / с.
При найденных значениях коэффициент вязкости k может быть определен по формуле. Эта цифра показывает отношение требуемой рабочей вязкости v1 к полученной рабочей вязкости v.
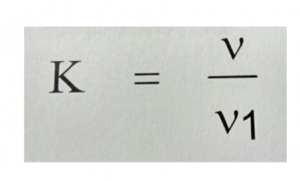
k = коэффициент вязкости
v = фактическая рабочая вязкость, ожидаемая для данных условий, мм ^ 2 / с
v1 = для фактического размера подшипника и рабочей скорости требуется кинематическая вязкость, мм ^ 2 / с
Значение k> 1 указывает на хорошую или даже очень хорошую смазку. Если k меньше 1, полное разделение металлических поверхностей не произойдет, и следует использовать смазки с добавками.
Шаг 4:
В данном примере коэффициент вязкости k равен:
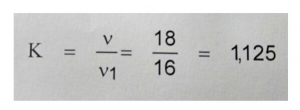
Это показывает, что выбранная смазка с точки зрения ее вязкости является хорошим выбором для ожидаемых условий эксплуатации.Ожидаемая вязкость должна обеспечивать достаточное разделение опорных поверхностей.
Шаг 5:
Определение коэффициента a iso
При значении k, полученном на этапе 4, для правильного продукта необходимо выбрать правильный выбор кривой.
Пересечение частного (e (c) * Cu / P) с соответствующей кривой дает искомый коэффициент a iso.